Qu'ont en commun la cape d'invisibilité d'Harry Potter, les uniformes portés par le prince William et le prince Harry lors du mariage princier de 2011 et le tissu dont est recouvert le Woolsack, le banc du lord chancelier à la Chambre des lords du Royaume-Uni ?
Ils ont tous été fabriqués par AW Hainsworth, une entreprise qui est le pouls battant de l'industrie de la laine au Yorkshire depuis sa création en 1783 par Abimelech William Hainsworth. Qualifier l'histoire de cette filature extraordinaire de « riche » serait un euphémisme risible. « Lors de la première guerre des Boers », explique le directeur du marketing par intérim Liam Conlin, « les soldats britanniques vêtus de rouge se faisaient remarquer trop facilement par les Afrikaners ; on nous a donc donné pour mandat de concevoir un uniforme de camouflage et nous avons développé un tissu appelé "le sergé kaki", qui signifie "poussière" en ourdou. »
Les efforts militaires de l'entreprise se sont bientôt étendus au-delà des tenues pour l'armée de terre : « En 1917, nous fournissions des uniformes pour la cavalerie cosaque russe », explique M. Conlin. « La Révolution arriva et la cavalerie fut dissoute, nous laissant avec tout un entrepôt de tissu bleu. Un an plus tard, en Grande-Bretagne, la Royal Air Force se sépara de l'armée et réclama une alternative au treillis kaki pour se distinguer. Hainsworth suggéra ce tissu : c'est de là que vient leur surnom de « Boys in Blue ».
Bien qu'elle produise toujours des uniformes militaires et de cérémonie, Hainsworth a aussi diversifié ses créations : le tissu de la filature est utilisé aujourd'hui par de grandes marques de mode et les amateurs d'opéra, de cinéma et de théâtre du monde entier peuvent l'admirer régulièrement sur les costumes des comédiens et des acteurs. Ils fournissent des tenues modernes au personnel des services d'urgence du monde entier et leurs superbes feutres sont utilisés sur les plus belles tables de billard ainsi que sur les pianos Steinway. Vous trouverez leur luxueux textiles dans les voitures Rolls-Royce et leurs couvertures étendues sur les lits des palais royaux d'Europe et du Moyen-Orient, ainsi que dans les chambres sacrées du Vatican. Ils conçoivent même une gamme de cercueils biodégradables.
L'étendue du répertoire de Hainsworth – allant du très fonctionnel au résolument utilitariste, en passant par l'ultra-décoratif – est facilité par l'intégration verticale. « Nous réalisons tout le traitement sur place, du mélange à la finition, en passant par le cardage, la filature, le tissage, le foulage et la teinture », explique le directeur technique Martin Howarth, qui est aussi chargé de l'achat de la laine, en nous conduisant dans la salle où commence l'ensemble du processus : un espace ressemblant à un entrepôt situé au rez-de-chaussée où des balles de laine tapissent chaque mur. « Nous possédons même notre propre laboratoire de test ainsi qu'une équipe de création interne. »
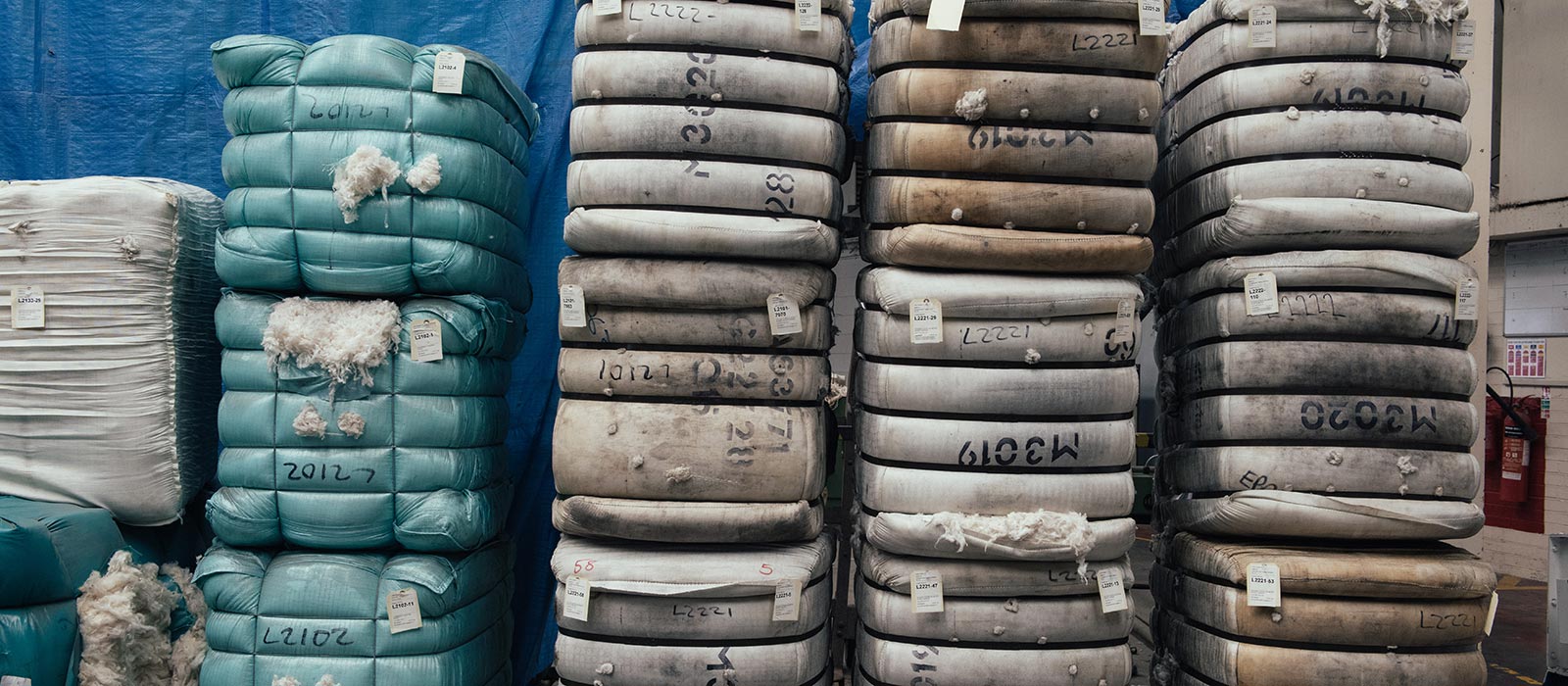
L'entreprise traite 6 700 kilos de laine par semaine, dont 3 300 kilos de fibre de mérinos provenant de 5 fournisseurs reconnus originaires du pays lointain d'où le Révérend Samuel Marsden a importé la laine pour la première fois en Angleterre, 24 ans après la création de Hainsworth : l'Australie. Mais c'est là où les choses deviennent un peu plus complexes : « Nous nous approvisionnons en 15 types de fibre différents, chacune ayant ses propres caractéristiques », explique Howarth. « Elles se distinguent les unes des autres par leur finesse, leur couleur, la quantité de matière végétale et la longueur de la fibre. »
Il s'agit d'une filature familiale. La personne actuellement chargée de l'achat de la laine, Roger Hainsworth, a endossé ce rôle il y a 25 ans pour succéder à son père. À travers les siècles, huit générations de Hainsworth et leurs employés ont fignolé, affiné et perfectionné les ratios idéals de différentes fibres afin de répondre au mieux aux exigences très variées de leurs tissus. « Nous travaillons désormais à partir de 22 recettes de laine mérinos », explique Howarth. « Il peut s'agir de 20 % de laine polaire de chez Swan Wool, de 25 % de mèches et de morceaux de chez United Wool, de 20 % de laine mérinos mélangée de chez Freemantle Wool et ainsi de suite. »
Hainsworth est une filature de laine et non pas une peignerie, ce qui détermine ses décisions d'achat. « Une peignerie utiliserait davantage de laine polaire plus longue », explique Howarth, « mais nous avons besoin d'une plus grande quantité de fibres plus courtes pour faciliter le processus de feutrage. » Le contrôle de la qualité est essentiel : « Nous comparons la laine aux normes historiques et l'examinons au microscope pour vérifier les écailles superficielles qui font office de petits cliquets lors du feutrage. »
Une fois rassemblés, les ingrédients de la recette sont mélangés : il s'agit essentiellement de mélanger les lots de composants et de carder la laine. Dans une filature de laine, le cardage est préféré au peignage car il permet d'obtenir un fil légèrement plus duveteux avec des fibres moins bien alignées. « Nous transformons la laine en flammé de fibres mélangées », explique Howarth en désignant une machine qui fonctionne comme une sorte de brosse à cheveux géante. « Nous obtenons une toile cardée qui peut être transformée en fil. »
Les mastodontes mécaniques qui nous entourent alors que nous visitons la filature sont incroyablement sophistiqués : un éventail vertigineux de rouleaux de précision, de bobines de condenseur, de broches tournantes et de magie automatisée. Howarth nous présente un monstre mécanique qui mesure le diamètre des fils en une fraction de seconde, élimine les sections trop larges ou trop étroites d'un nanomètre, puis raccorde les deux morceaux de fils avec des bouffées d'air précises qui ré-enroulent le fil. Certains des équipements de tissage peuvent réaliser 350 insertions de trame par minute, tandis que le métier à tisser pour jacquard peut entremêler la trame et la chaîne si étroitement que le tissage de n'importe quel visage célèbre serait instantanément reconnaissable.
Gallery
Après le tissage vient l'étape du foulage et du feutrage, durant laquelle le tissu est compressé en le serrant entre d'énormes tablettes en métal ressemblant aux mâchoires du Léviathan, qui le compriment dans un torrent d'eau bouillante savonneuse. Enfin, les feuilles rétrécies sont teintes, coupées et pressées pour obtenir le produit final. Le tissage à lisière sur la bordure indique fièrement en grands caractères : « Fabriqué en Angleterre par Hainsworth ».
Du début à la fin, le processus nécessite plusieurs semaines de main d'œuvre hautement qualifiée. Mais le travail de Hainsworth repose sur bien plus que les artisans qui s'affairent par cette chaude matinée de juillet. Une exploitation telle que celle ci constitue une mine d'expertise, d'inventivité et d'ingénuité accumulées au fil des siècles. Le temps présent n'est qu'un point d'ignition narratif dans le besoin historique de l'humanité de transformer la laine en un tissu encore plus élégant et fonctionnel. En visitant une telle installation, il est passionnant de réfléchir aux riches chapitres qui restent à écrire.